Publications
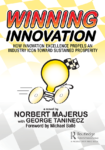
Winning Innovation: How Innovation Excellence Propels an Industry Icon Toward Sustained Prosperity
A novel by Norbert Majerus with forward by George Taninecz
An engaging business novel, Winning Innovation dives into the art and science of innovation; the thrills of the European bike-racing circuit; the vibrant landscape and cuisine of Italy; and a cast of intriguing characters who work to put Davanti on the road to sustained prosperity. The company’s leader isn’t afraid to learn and apply new ideas to reenergize his company, and finds he cares more about his employees than he could ever imagine. A young innovator struggles to see a product idea to fruition as well as rise into management — and he falls in love along the way. A newly promoted R&D director brings teamwork and transparency to product development and aligns the entire company around innovation.
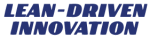
Common Sense Lean: You Can Only Sell What You Have! by Norbert Majerus
July 2019
If I was selling goods on line that I do not have, I might go to jail. Or if I commit to providing a service –
like fixing somebody’s roof this week – knowing I am unable to perform, I could get in trouble. And
rightly so, because I would be deceiving customers and breaking the law.
Although most corporations do a good job delivering goods and services to external customers, but they
lack those same standards for internal customers. For example, a department responsible to test
prototypes may accept more requests for tests than they have capacity for and they fail to deliver on
time. Or an R&D organization is late designing a new product because they accepted targets that they
cannot meet.
Why does this happen?
I was taught in my corporate career that you can never say “no” if you are asked to do something. And if
an executive challenges you to move up the project delivery, it don’t challenge the executive with
excuses like not having the resources. I also learned that it is good to have a backlog because you can
batch jobs and be more efficient. After all, being behind and “needed” is the best assurance against
budget cuts.
But what does it do to the company?
Many companies do not know how much money they lose by late internal deliveries. Late product
introductions can cost millions and every day a plant waits for a new piece of equipment due to a
limited budget can drag earnings down by an amount that dwarfs the additional funding.
Here are a couple of remedies that I have used:
– Know the cost of delay for all work – that helps make the right decisions for investment and
resource allocation
– Make the capacity visible to everybody so people can see and understand – this communicates
to everybody involved if capacity is available or needed
– Do not plan for 100% of the resources – things will go wrong and the buffer helps to remain on
schedule
And if you call it common sense rather than “lean” you may have less resistance implementing it.
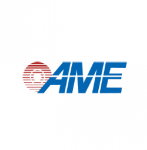
Making the Case for Lean Project Management from Target Magazine
Summer 2019
Lean has become a popular adjective to so many things: manufacturing, innovation, startups, services, health care. So why not “lean project management”? For some, lean project management means merely creating a Toyota-like chief engineer position. But lean project management takes a framework, skills, training and often a different organization. It is the combination of lean thinking and good traditional project management practices—a powerful synergy that leads to amazing results for virtually any type of project.

Don’t Retire Your Knowledge – Reuse It from The Lean Post
October 25, 2018
As baby boomers like me are retiring, companies are wondering how to retain the knowledge that walks out with them. At my recent retirement celebration, a company executive complimented me on my unique expertise and the knowledge I created over 39 years. Fortunately, some of my knowledge remains in the company because it is summarized in a book, Lean-Driven Innovation: Powering Product Development at The Goodyear Tire & Rubber Company. But that is only a small part of what I’ve learned over the years – the rest now resides with me.

BTOES Exclusive Slide Deck: Lean-Driven Innovation from BTOES Insights
September 5, 2018
Courtesy of Good Year, ‘Lean-Driven Innovation’ Jean-Claude Kihn and Norbert Majerus have written an article introducing their presentation. Read the full article at BTOES Insights.
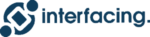
Developing New Products at Pit Crew Speed
July 13, 2018
If you google “pit crew” you will find dozens of movie clips from the 5 minute stop in the 1950’ies to the 2 second stop at a recent Grand Prix. Learning, continuous improvement, better tools and training made this possible.
In the early clip, one tire changer hammers away at the nuts and changes one tire at a time. This reminds me of the way we used to design tires at Goodyear, except that at Goodyear R&D, the one lonely tire changer would have serviced at least 3 cars at the same time.
Today Goodyear works more like the Melbourne Grand Prix crew that changed 4 tires in a couple of seconds.
“Wait a moment” – you will tell me: “those guys work for 2 seconds and then the crew of 20 sits idle until the car comes back next time – what a waste!” My answer is that if they can shave a few tenths of a second off the stoppage time, it can lead to victory, which is well worth the investment.
The same is true for managing R&D and innovation projects: what really matters is being the first to market. If there is a single engineer on a project and the engineer multitasks and shares his/her time between many projects, the engineer may always be busy (efficient use of engineering resources) but the project will have a long cycle time and the company will most likely lose the “race to market”.
Time to market is just as precious for R&D projects than it is for car racing. A few weeks lost, can cost the business millions of dollars and a few months lost can mean second place in the race for market share.
The lost business income most often dwarfs the cost of a few extra resources who work in pit crew mode to shave as much time off the development time as possible. At Goodyear a major project was moved up 6 months by sending a “crew” of more than 20 engineers to a plant for a week to build 24 prototypes.
In addition to R&D, some companies train their teams in “pit crew” operation like airlines who can increase the time in the air of the planes by a very significant amount by turning them around faster on the ground. Watch the action next time you wait for your plane; with some airlines it resembles a real pit crew.
One of the reasons why agile and sprints gain popularity is that R&D organizations start understanding the cost of time and the basic working principles developed by pit crews.
Ben Cook, Director of Programming and Pit Crew Recruiting at PIT Instruction and Training educates and trains racing pit crews in Charlotte NC. Ben says that you do not start with speed – you start with a good process and good skills. Speed comes as you learn and get better.
Jean-Claude Kihn sponsored a project called “Pit crew” at Goodyear R&D in 2012 when he was the CTO. The project reduced the cycle time of a tire development iteration by 50%. “After all the years Goodyear has spent in racing pits, it was time to apply what we learned there” says Jean-Claude
Ben Cook and Jean-Claude Kihn will share their ideas with Product developers and innovators at the LPPDE North America (Lean Product and Process Development Exchange) at Ohio State on October third 2018.
Watch webinar recording with Norbert Majerus about Lean Driven Innovation. He takes us through the highlights and key learnings of the Goodyear transformation to being an innovative Lean Product Development organization.

Lean Principles Apply to Fuzzy R&D Too from The Lean Post
March 15, 2018
Although lean thinking has been accepted and successful in manufacturing and many service settings, such as healthcare, there is still a lot of angst associated with applying lean to the creation of innovative products and services. The concern starts with a fear that lean stifles creativity, which contributes to low success rates, and, at best, results in minor cost reductions within product and service development. Read more at lean.org.
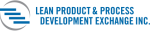
The Importance of Structure in Innovation from Lean Product and Process Development Exchange
September 5, 2017
In the early parts of this century, Lean, especially lean-sigma came under intense criticism: An article in the Forbes magazine (Norbert Majerus, Lean-Driven Innovation, CRC Press, 2015) documented results, mainly from 3M, which indicated that lean – or at least lean-sigma – was detrimental to innovation. Indeed, 3M’s index of innovation (income from products less than 3 years old) had fallen from between 30% and 40% down to single digits. Read the full article at lppde.org.

Riding the Goodyear Wheel to Innovation Excellence from The Lean Post
July 26, 2017
Many readers will think: “This all seems like a manufacturing process — wasn’t this supposed to be an innovation creation process?” The answer is, “Lean principles are universal — they apply everywhere.” Read the full article at lean.org.
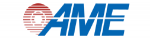
The One with the Most Tools Wins! from AME Target Online
April 12, 2017
I recently saw a blog that described 32 lean tools. I thought, “Wow, 32 tools! That is a lot more than I know.” What tools am I lacking? Which tools are missing from my lean toolbox? I did not read the article.
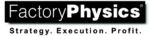
Finding Science and Success with Lean Principles in R&D from Factory Physics
February 2017
Norbert Majerus, Lean Champion at Goodyear Tire and Rubber, provides a guest blog relating his journey in applying Factory Physics concepts to guide Goodyear’s Product Development Lean journey. As Norbert writes, “When we first came upon Factory Physics, about half of our R&D projects were unprofitable. Today, nearly all projects confirm the positive business case that justified their start in R&D, and in 2015 Goodyear’s operating income exceeded $2 billion.”

How We A3 at Goodyear from The Lean Post
October 18, 2016
Goodyear has expanded where and how it uses A3 thinking.
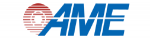
Goodyear Will Leverage The AME Excellence Award Process For Continued Improvement by Norbert Majerus from AME Target Online
September 14, 2016

To A3 or Not to A3 from The Lean Post
February 9, 2016
Most engineers like structure, process, and standardized forms; especially as a way of applying order when situations seem to be losing theirs. It is this element of standardization that many find appealing —confidence and comfort amid familiarity. Some people also like “one-size-fits-all” tools but they are not always happy with the fit.
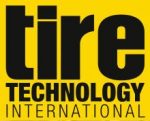
Lean Possibilities in R&D from Tire Technology International
November 9, 2015
Goodyear’s decade long implementation of lean R&D practices has led to a steady increase in innovation capabilities and capacity without additional investment.
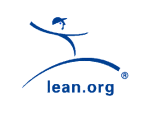
Bringing Lean Thinking to R&D at Goodyear from Lean Enterprise Institute
August 11, 2015
Why and How to use lean in R&D